Designing Custom Sheet Metal Brackets for Under-the-Hood and Interior Use
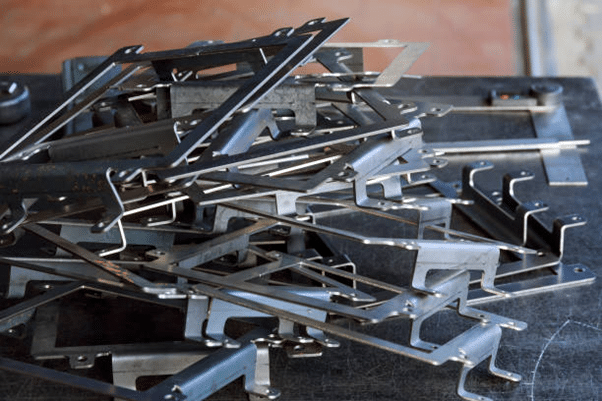
Durability and precision are non-negotiable in a vehicleโs design. Custom sheet metal brackets are custom parts of a car that are used on the vehicleโs interior and under-hood components. They enable the vehicle to function properly by ensuring that major systems and parts are secured, providing vigor and structural stability to the vehicle. Businesses operating in the automotive sector should know the steps and the significance of making custom design sheet metal brackets.
This article will discuss how factories that deal with the manufacture of custom brackets made of sheet metal design these brackets for the vehicular under-the-hood components and interiors, addressing relevant instructions pertaining to design specification, materials, and manufacturing, as well as new innovations with an emphasis on increasing quality in the process. Customization of vehicles is at the center of emerging technologies in the automotive sector so the factories must also adopt modern methods to compete.
The Role of A Sheet Metal Factory in Automotive Design
Brackets custom made from sheet metal are integral to the automotive industry. This is why automotive engineering companies depend on specialized factories for the production of custom sheet metal brackets. These factories perform essential functions that help the companies build parts which are tailored in terms of performance and durability. The automotive industry as always has needs that are incredibly sophisticated pertaining to structural and non-structural functions of custom brackets. As a result , precision is of utmost importance.
In the automotive world custom sheet brackets have many functions. Different components are attached like an engine, air conditioning units, exhaust systems, and even electronic systems. These brackets need to be custom made and as a result a sheet metal factory is equipped with advanced technology like CNC machines, stamping presses, and laser cutters. Beyond just production, these factories are crucial in the design phase ensuring maximum strength, flexibility, and compatibility of the brackets with vehicle components. This teamwork guarantees that the high level effectiveness of the brackets along with rigid safety standards is always sustained.
Key Design Considerations for Custom Sheet Metal Brackets
Designing custom sheet metal brackets has many considerations from meeting safety requirements to functionality and product as a whole. Some important considerations are material specification, thickness, strength and fit. The brackets ought to sustain the mechanical stresses from vibrations, temperature fluctuations, and pressure during operation, particularly when placed in the vehicleโs interior or under the hood.
Consider the design process of the bracket for its intended purpose. Custom sheet metal brackets designed to provide support for an engine component located under the hood gets exposed to high stress and temperature conditions. Therefore, such brackets should utilize highly durable materials, like stainless steel, or aluminum and should be crafted with great precision to ensure they occupy the minimal spaces available under the hood.
When creating custom machined brackets to be used within the vehicle cabin, the design should also focus on the entire vehicle aesthetic and cabin organization. In addition to meeting functional objectives, these components integrate both seamlessly with the vehicle and other parts.
Successfully balancing form and function allows the bracket to perform its intended role without interfering with the appearance or functionality of the vehicle.
Manufacturing Techniques Used in Custom Sheet Metal Bracket Production
When choosing the layout and materials of custom sheet metal brackets, the CNC bracket shop and sheet metal fabrication shops will use a combination of techniques to manufacture it. These include the conventional methods of punching, bending, and welding along with modern techniques like laser cutting, water jet cutting, and CNC machining.
With precision laser cutting, a sheet metal factory is able to achieve high detail and cut complex shapes, which drastically minimizes material waste. That is especially advantageous in the automotive industry where weight reduction is critical. For high-performance automotive parts, CNC machining is a preferred method as it ensures custom sheet metal brackets are produced within strict tolerances.
The method for producing brackets is selected based on the design complexity of the bracket, the material to be used, and the required quantity to be produced. Small batch production needed for prototype designs is just as easily adapted to as large scale manufacturing for mass production. This flexibility makes sheet metal fabrication shops highly versatile. Moreover, these techniques improve efficiency which reduces costs, improves speed while maintaining quality, and precision in part production.
Innovation and the Future of Custom Sheet Metal Bracket Design
With the advent of new technologies, there is an increased demand for highly efficient, long lasting custom sheet metal brackets in the automobile industry. The same industry which uses custom sheet metal brackets will also custom design them with 3D printing and smart materials which will advance in the future. It is essential for clients that metal sheet factories keep up with these trends.
Alongside the advancement in automobile features comes the advancement in metal brackets as they will need to anticipate new smart systems, sensors and communication devices for autonomous driving vehicles. There is also a need for a new framework with the shift towards electric vehicles (EVs) as they use electric batteries and require unique designs for controlling the electric drivetrains.
To keep up with those changes, many factories have started using new automation technologies for precise and efficient production of electric vehicles. These improvements will meet both the volume and mechanical requirements for custom sheet metal brackets. In order to keep a competitive edge in the market, factories will have to quickly evolve and innovate alongside the changes.
Conclusion
The creation and design of specific automotive brackets involves custom sheet metal fabrications and is integral to the performance, safety and life of every automobile part. The various applications prerequisites, including those found under the hood and interiors, require sophistication which is provided by specialized subcontracting manufacturers or precision sheet metal fabricators who have sophisticated tools and techniques as well as high-grade materials. These factories are crucial for the modern vehicle design because they assist with the selection of techniques and materials including custom brackets made out of specific metals and ensuring they are made with the utmost precision.
In the context of the dynamic automotive industry, it is undeniable that all operations which involve subcontracting manufacturing precision metal fabrications will undergo change as vehicle production technologies change. With the capabilities as well as the expertise which is put in the design and fabrication of custom brackets out of specific sheet metals, it greatly assists with the automotive emphasis in engineering;s innovation pioneering.
Observer Voice is the one stop site for National, International news, Sports, Editorโs Choice, Art/culture contents, Quotes and much more. We also cover historical contents. Historical contents includes World History, Indian History, and what happened today. The website also covers Entertainment across the India and World.
Follow Us on Twitter, Instagram, Facebook, & LinkedIn